Existing subsea production and injection experience a number of issues with the production and annulus pressure barrier valves (e.g. PMV, PWV, AMV and AWV). These valves form the primary and secondary barriers between production fluids and the atmosphere. Problems start occurring after several years of continuous production. One such problem is that of degradation and failure the actuator springs on the production and annulus valves. The degradation is progressive and eventually results in inability to function the valves. Up to now, the only measure available to the operation was to shut in the Christmas Tree (XT), and hence the well, and recover the XT to the surface. The XT would either be refurbished with new valves and actuator, or a new XT would be required. Either of the two options results in very costly loss of production revenue, as well as costs associated with recovering, refurbishing and replacing the XT, followed by costs associated with installation campaign.
MMA has developed an innovative Subsea Valve System (SVS) that reinstates the full functionality of the XT without having to refurbish or replace the XT and with significant reduced production down time. The SVS incorporates dual barrier production and annulus valves complete with associated spool pipes. If required, a cross-over valve is also provided. In essence, the system provides a complete new production and annulus pressure barrier system, with the existing failed valves being locked permanently open. The SVS is designed to be attached permanently to the XT frame and is deployed subsea by divers. A novel alignment system is incorporated to compensate for any XT flange misalignment to the SVS system. Actuation control of the individual valves is facilitated by rerouting control fluid supply from the existing failed valves.
The SVS provides a further 15 to 20 years extension to operational life of the XT. Two systems were successfully installed and are operational. A third system was deployed in late 2018.
Our scope of supply included:
- Flow assurance analysis to identify pressure loss, erosion risk and vibration-related issues. The analysis includes multiphase Computational Fluid Dynamics (CFD) to quantify flow-induced vibration forces.
- Finite element analysis (FEA), including thermal and pressure-vessel analysis, to ensure structural integrity and adequate fatigue life
- Design for manufacturing, including tolerance stack-up analysis, to guarantee correct subsea fitting and interface
- Interfacing with client, OEM’s, third-party verification bodies, assurance bodies and vessel personnel
- Manufacture, assembly and qualification testing of full system in compliance with API 6A
- Design and manufacture of installation template and subsea alignment system to minimise offshore installation time and maximise fitting accuracy
- Design, analysis and manufacture of associated lifting equipment, overtrawlable and dropped-object protective frame, and cathodic protection system
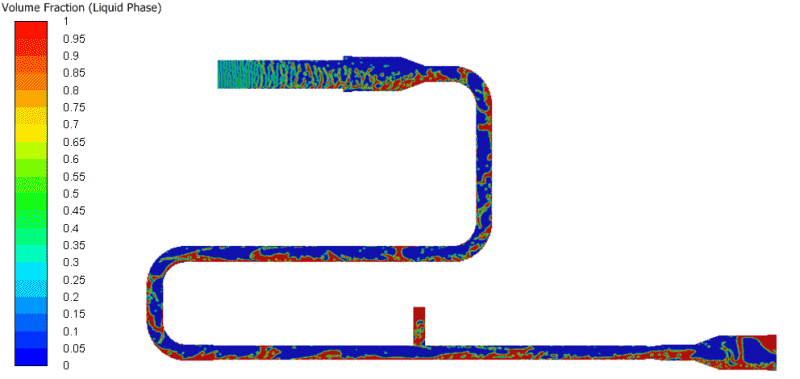