Project Overview
The Ichthys Mooring Equipment Project conducted at the MMA Batam shipyard facility is another example of MMA’s capabilities. The project involved the receipt of three barge shipments of heavy and difficult to handle mooring equipment that needed to be offloaded, transported and stored within the Batam facility. The Project involved two other Ichthys Project contractors, all operating to the highest Project standards.
The cargo varied on each barge shipment and brought different challenges in relation to the lifting and transport methods required to complete the work. Complex lifting and transport methods were developed for each task to deal with the different nuances that the different cargo components posed.
Heavy lift equipment was provisioned from one of MMAs preferred contractors out of Singapore. A single barge was used to transport two large crawler cranes and SPMTs (Self Propelled Multi-Axle Trailers) to Batam. The cranes and SMPTs were assembled on site, and once assembled the equipment was put through a stringent testing regime to ensure compliance with one of MMAs critical controls (lifting operations).
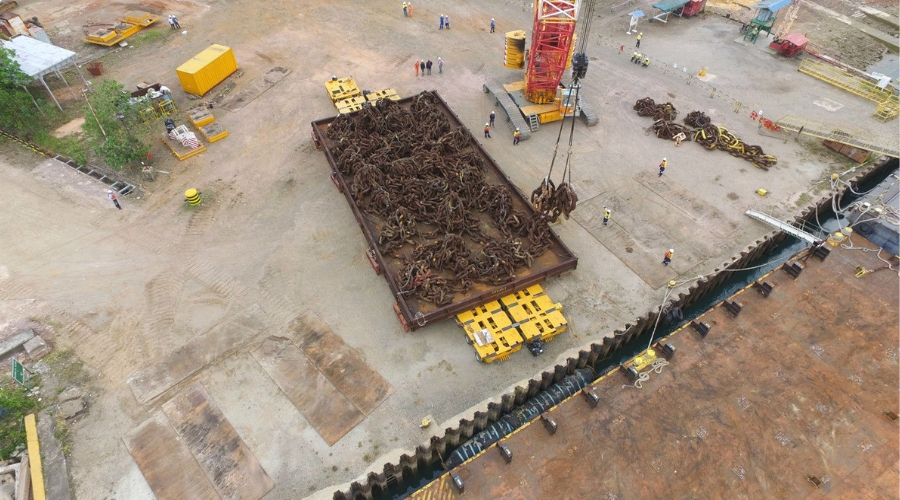
Cargo shifted:
- Two 800 tonne lengths of 150 mm mooring chain;
- Three 75 tonne umbilical reels;
- Gangway landing platform (11mx 8mx7m) 37 tonnes;
- Four 70 tonne mooring pile sections; and
- Miscellaneous project equipment.
The first barge contained the two large lengths of mooring chain and was berthed at the land backed heavy lift wharf approximately 12 hours prior to unloading. The mooring chain sea fastening was removed and ballast tank hatches removed and large ballast pumps installed in preparation for off-loading activities. A single 100 tonne transport basket was fastened to the SPMTs and then rested on stiff leg stools to ensure the transport basket was secure during loading.
Both chains were in continuous lengths, to move the chain from the barge to the transport basket it required the cranes to work in unison, with both cranes seeing loads of between 35 – 40 tonne as the catenary of chain between the two changed during the lifting process.
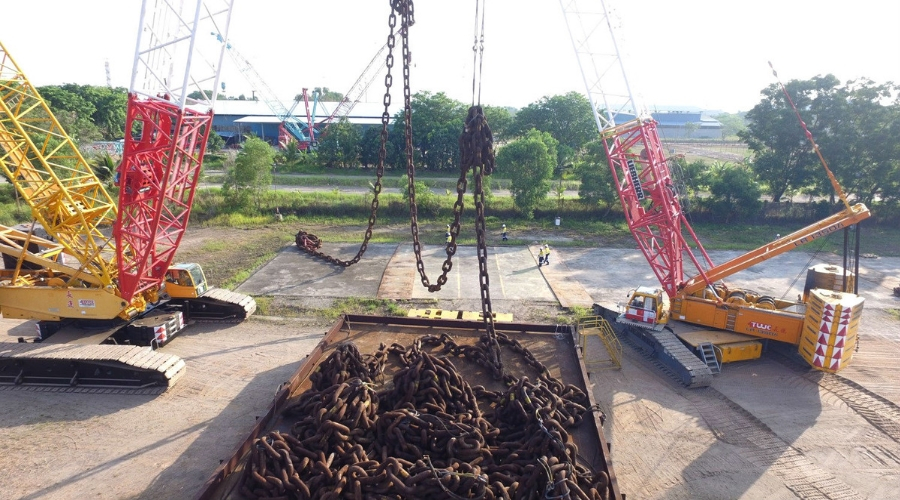
Once the complete chain was positioned on the basket, the SPMTs were jacked up so the basket was clear of the leg stools to commence the placement to the laydown area. Both cranes were tracked up to the laydown area and positioned for the unloading activities. Finally, once the SPMTs had positioned the transport basket correctly the basket was jacked down onto the leg stools for unloading activities. The Project was only completed upon successful demobilisation of the cranes and SPMT to Singapore.
The entire project was completed ahead of schedule and without incident.
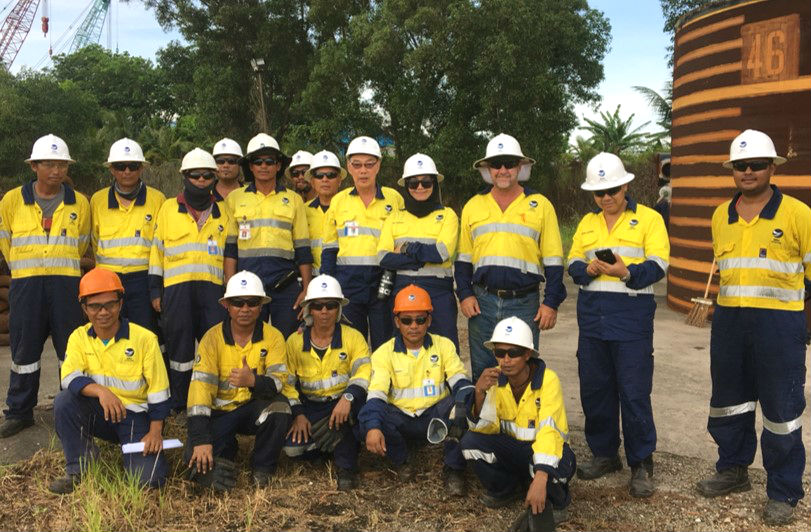