Project Overview
Fatigue cracking of the K Joint had occurred below the waterline and flooding between the ocean and the annulus was observed. Strengthening and corrosion mitigation was critical to maintaining the leg’s structural capacity.
MMA's Solution
We worked with the client and Worley Parsons to deliver a high strength grouted connection between the jacket leg member and an internally placed mandrel. MMA is a licensed BASF applicator, so we specified the BASF Masterflow 4510 grout - a cementitious, high strength, 80MPa, non-shrink, deep pour, precision grout. The grout was placed within the platform leg in an annulus between the leg and a mandrel specially designed to reduce the volume of grout required and allow future inspections of the leg internals below the repair location.
We built and tested a full-scale mock-up of the platform leg and mandrel at our Henderson facility. This testing was critical to demonstrate the flowability of the grout around the mandrel.
Outcome
As the pour was to be started partway up the jacket leg the bottom of the mandrel needed to seal against the leg to hold the grout in the annulus. This seal was to be achieved via a third-party supplied inflatable packer.
However, the initial inflation failed and there was no contingency procedure for sealing the annulus. This required the team to return the mandrel to shore to install a new inflatable seal. During this time, we took the opportunity to design and fabricate a contingency seal that could be inflated simply using grout in the event that the inflatable packer failed again.
The installation of the grout inflatable seal onto the mandrel was quite challenging as the mandrel was not designed for such a seal but we believe that this grout inflatable seal was a much simpler and more robust solution which was proved with an onsite trial.
The entire contingency seal design, fabrication, testing and mandrel installation took us just one week.
Key Equipment / Installation Method
- MMA's high-capacity Single Pan Mixer (SPM5000)
- Bespoke packer bags for sealing annulus
MMA Innovation / Value Added
High-performance grout injected into WHP leg has significantly extended the design life and all on-site works were completed in one week, ending the shutdown of the WHP.
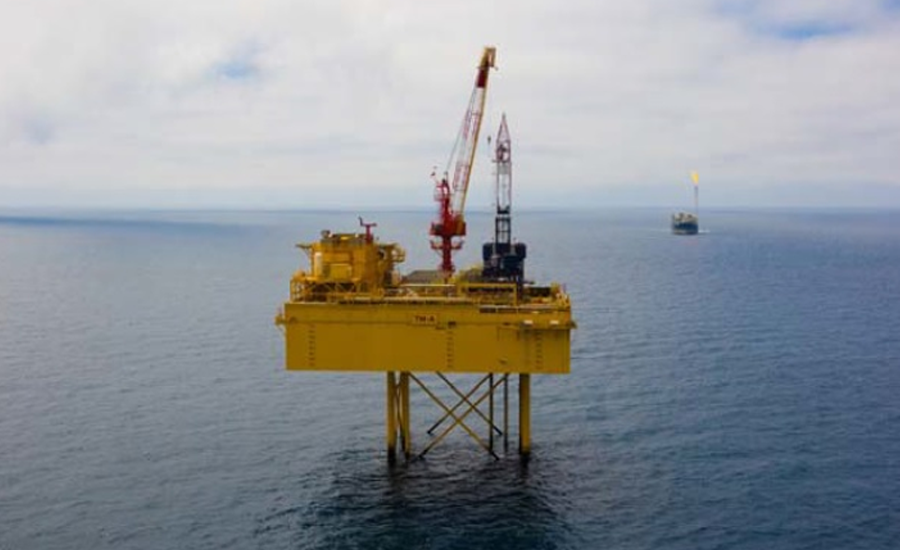